We are in the midst of an unprecedented global crisis – one that is turning out to be more severe than any of us might have anticipated. As we grapple with the emerging realities of the situation, it is evident that we will all be acquainted with a “new normal” once this is behind us. Although several industries have been adversely impacted, the technology sector has responded with briskness by rallying around the idea of collaborating remotely.
However, the manufacturing sector has been impacted severely as it bears the brunt of a complete lockdown. The differing realities of the technology and the manufacturing industries are perhaps best summed up by the completely opposite perspectives offered by Mark Zuckerberg and Elon Musk on the quarterly earning calls of their respective companies.
Keeping aside Mr. Musk’s demands to “FREE AMERICA NOW”, the reality is that manufacturing companies will resume operations sooner or later. While some industries may face a reduction in demand, there are several others, like those that manufacture essential goods, that will see an uptick.
This would mean that smart factories will have to get smarter to ensure higher levels of productivity than before while maintaining the stringent new norms of social distancing and worker safety.
Table of Contents
Smart Factories in a Post COVID World
As factories respond to a new environment that is markedly delicate, intense and fragmented, they will need to focus on three important aspects.
- Safety of the workers
- Optimal Operations and Capacity Planning
- Efficient Remote Operations
Let us look at how technology can enable businesses to operate smart factories that are attuned to each of these areas.
1. Safety of Workers
Maintaining Social Distance while performing tasks on a factory floor will be key to worker safety. While policies can be formulated to ensure social distancing, technology solutions can go a long way in ensuring compliance and alerts. Manufacturing companies can look at –
- Creating segregated workspaces to avoid employees assembling in large numbers.
- Deploying connected sensors and cameras to ensure mandated distance and alerts in case of violations.
- Use analytics to schedule and plan breaks, carry out machine maintenance and stagger common gatherings such as lunch breaks.
- Train the staff to effectively use video conferencing as primary mode of communication even within the premises.
2. Optimal Operations and Capacity Planning
The global economy is marred by uncertainty and most large organizations have withdrawn their guidance for the rest of the year. Considering there can be massive fluctuations in the demand for goods or in the supply of raw materials, it becomes imperative to use data and analytics for the forecasting and planning of operations.
For those manufacturing companies that are yet to invest in Digital Twin and Digital Thread, there cannot be a more opportune time. These approaches can help in the simulation of various scenarios, enable preventive maintenance, and help with skill planning. This can in turn help in the optimization of operations by planning optimal capacity for a wide range of scenarios which can’t be easily analyzed otherwise.
3. Efficient Remote Operations
To the extent possible, organizations should employ remote operations to minimize the number of people required on the shop floor. Thankfully, with the advent of technologies such as Machine Vision and AR / VR, a number of tasks can be carried out remotely without compromising on quality. Here are a few examples –
- Training of employees through VR replicating virtually a presence which is almost as good as being in the plant.
- Highly skilled and expensive resources like SMEs and supervisors need not be physically present in all the plants owned by a business. With AR and other data captured by sensors, they can carry out inspections remotely and provide crucial inputs.
- Remote troubleshooting and guided maintenance can further help in reducing visits from equipment vendors and significantly reduce maintenance costs over the long run.
- Automated and remote quality inspection through image analytics and computer vision.
We may be facing difficult times but as is often said, “in the middle of adversity lies opportunity”. And the opportunity is now for one of the oldest and most important industries to use this unfortunate intervention to accelerate their digital transformation. It is time now for manufacturing to get a whole lot smarter.
Author’s Bio:
Dharmraj Jhatakia
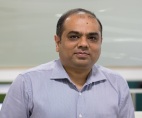
General Manager – Product Engineering Services Happiest Minds Technologies
Dharmraj is a General Manager with the Product Engineering Services division at Happiest Minds. He has a keen interest in understanding the challenges faced by companies in the industrial market segment and conceptualizing services that can deliver sustained business value. He also keeps a close watch on how disruptions such as IoT, AR/VR, Analytics & Machine Vision can help industrial entities in creating differentiation that can lead to a competitive advantage.